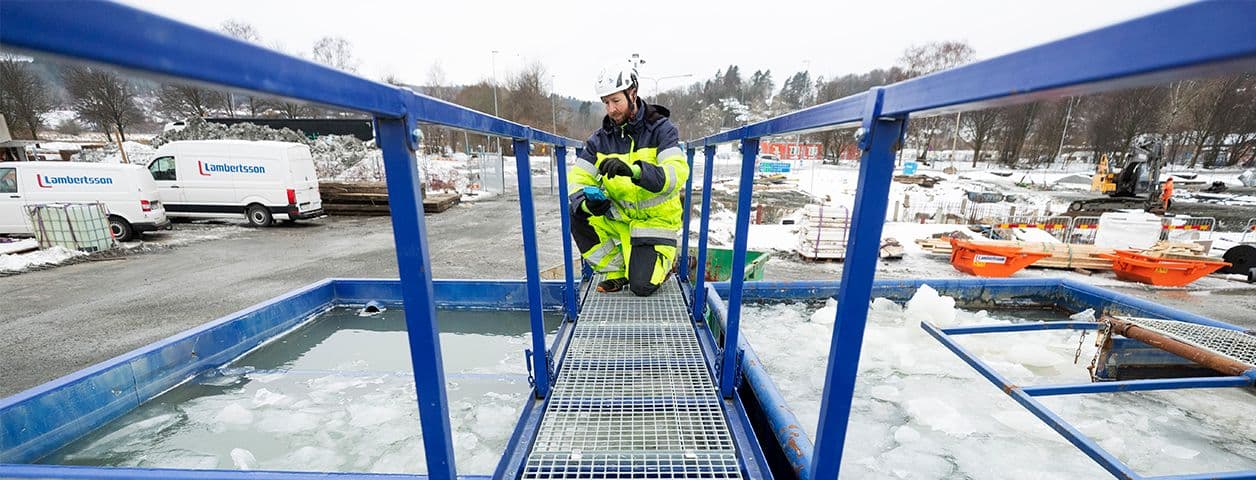
Drilling sludge posed challenges for Peab in Kållered
Drilling sludge and stringent water treatment requirements nearly caused complications for Peab during the construction of a large warehouse in Kållered. Traditional methods proved insufficient.
Peab is actively constructing a new warehouse in Kållered, slated for completion in 2020, emphasizing environmentally friendly solutions in both construction and operation. The groundwork spans an area of 28,000 square meters, involving the drilling of approximately 160 holes for geothermal heating.
It was these holes that caused Peab concerns in January 2018 when construction commenced. The boreholes needed to reach a depth of a couple of hundred meters, where saltwater leaked in from the bedrock. Drilling sludge, i.e., the rock flour and gravel left when drilling into the rock, turned the water in the holes into a murky mess.
Simultaneously, the City of Mölndal imposed strict requirements that all water leaving the construction site and discharged into stormwater had to be completely clean since it flows into a stream. And it was a significant amount of water, 100 cubic meters per day, something regular sedimentation containers couldn't handle effectively.
At that point, the site manager contacted sister company Swerock, which recommended Swedish Hydro Solutions. The chitosan treatment equipment was not what the installers had anticipated.
– We thought we would get twenty containers, and then they showed up with a small trailer, a steel tub, and a few socks, says worksite supervisor Tony Elggren.
It took a few weeks before everything functioned satisfactorily. The salt in the water disrupted the chemical process with chitosan, which causes the drilling sludge particles to flocculate. The solution was to pH-adjust the water using carbon dioxide and add a supporting dose of polyaluminum chloride, which facilitates flocculation in case of elevated salt levels in the water.
– You can see in a second how it starts clumping together and sinking to the bottom, says Tony Elggren.
Afterward, the water passes through the chitosan socks and continues to sedimentation tanks and filters. Mölndal City's requirement is that the suspended material content in outgoing water should be below 25 mg/l. The content in incoming water at the Kållered construction site varies from several hundred mg/l to over 1000 mg/l, and after treatment in Swedish Hydro Solutions' purification plant, the water content averages 15 mg/l.
Tony Elggren measures the particle content once in the morning and once in the evening, adjusting the amount of polyaluminum chloride needed. He changes the chitosan socks himself. The ongoing service is not more complicated than that, and he handles it seamlessly.
Tony Elggren's work primarily revolves around ensuring the logistics of the water flow function. The water from all pumps on the construction site is buffered in a reservoir before proceeding to chitosan treatment. It must be a consistent flow to and from the reservoir to avoid any stoppages that might halt work.
The geothermal holes are drilled and finished at this point, but there is still a significant amount of excavation water with clay soil that needs purification. Tony Elggren envisions that high standards will become the norm in the future, and contractors won't be able to rely on traditional water treatment to a large extent.
– In a workplace of this size with substantial water quantities, you can't wait for sedimentation to get it clean, says Tony.
He believes that Peab will continue on the current path.
– Sure, it costs money and takes some time. But I still have to say it feels good that the water we release into the stream is completely clean - even cleaner than what's already flowing there.
More projects
Need more information?
If you're seeking more insights about our projects implementations or want tailored guidance for your unique requirements, get in touch with our water treatment specialists.