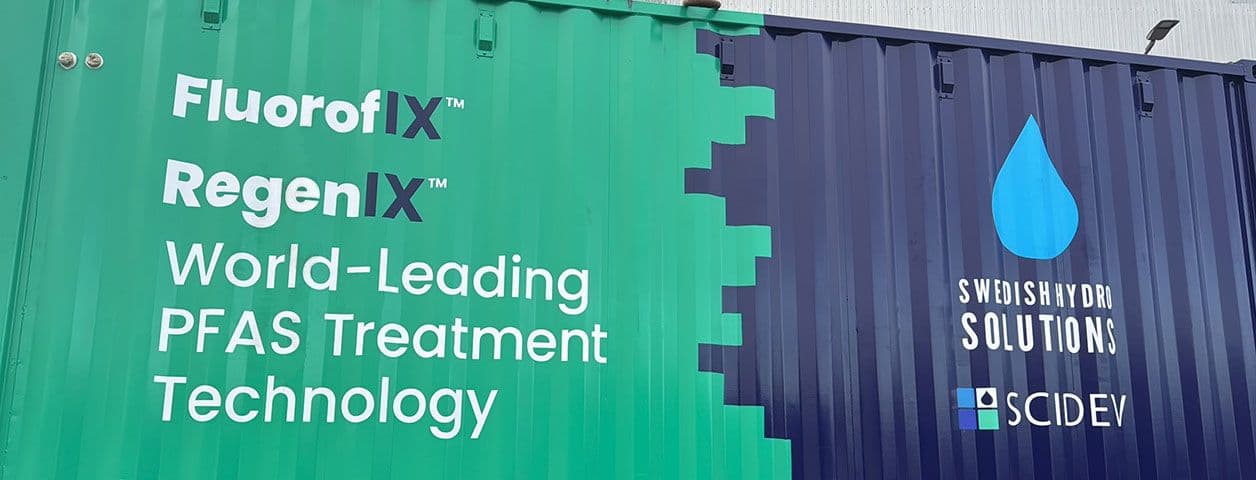
PFAS treatment delivered to an energy company
25.01.14
Earlier in 2024, an energy company received approval to continue discharging its treated leachate into the municipal wastewater treatment plant. Consequently, the company was required to carry out an investigation to explore options for reducing PFAS levels in its water. To fulfill this requirement, the company initiated an evaluation of technical, environmental, and economic alternatives.
As part of this evaluation, Swedish Hydro Solutions was commissioned to conduct a bench study during October and November to identify suitable treatment technologies. The bench study led to the development of a pilot plant, which was delivered in the second week of January. The full-scale plant will now be tested until March to evaluate how effectively it reduces PFAS emissions and other pollutants from the energy company. This test period is a crucial step in finding a sustainable solution to reduce the company’s environmental impact and the ongoing costs associated with leachate treatment.
– In recent years, we have built substantial experience in projects aimed at reducing PFAS-contaminated water while developing a deep understanding of various practical solutions. This has enabled us to offer a wide range of tailored methods depending on the PFAS composition in the water and other contamination challenges, says Carl-William Kalholm, Sales and Marketing Manager at Swedish Hydro Solutions.
– For more challenging water with a high presence of so-called short-chain PFAS, we use multiple filtration steps to optimize the total project cost, with the core being lead-lag filters with ion exchangers, Carl-William adds.
Pilot facility with multi-stage filtration
To identify the most suitable treatment technique for the energy company's needs, a bench study was conducted where selected techniques were tested in a laboratory environment. The study resulted in a plant design for the pilot project, which includes the following technologies:
- 10-foot technical container for sedimentation/flocculation
- Flocculation mixer with a 4 m³ capacity, including the possibility for pH adjustment
- Lamella separator with a surface area of 40 m²
- 20-foot filtration container with multi-stage filtration, including zeolite, activated carbon, and ion exchange filtration